- Inspección en Linea (Herramienta MFL)
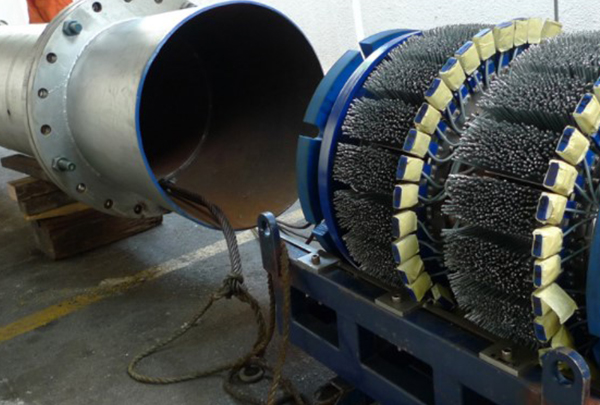
Contamos con la representación de una transnacional especialista en inspección con herramientas inteligentes, nuestras herramientas de inspección en línea de fugas de flujo magnético de alta resolución están diseñadas para proporcionar la información más precisa sobre la condición de la tubería y las características relacionadas con la integridad.
El uso de tecnología de sensor superior y capacidades avanzadas de adquisición de datos aseguran que nuestras herramientas registren y entreguen datos de encuestas de alta resolución del 100%.
Nuestra herramienta MFL es robusta y fiable para soportar el agua de mar, gas agrio, dióxido de carbono, amoníaco, alta presión, alta temperatura y otras condiciones de operación hostiles.
Nuestras herramientas de inspección MFL de baja fricción son ideales para gasoductos de baja presión o en múltiples fases.
Esta flexibilidad operativa se traduce en mayores tasas de éxito de primera ejecución, menores costos en la ejecución de herramientas de encuesta y menos tiempo de inactividad para la tubería.
- Gerenciamiento de Integridad
Desarrollo de Sistemas de Gerenciamiento de Integridad (SGI), cuyo objetivo es la generación de planes de gestión mecánica y confiabilidad, los cuales permiten optimizar y prolongar el tiempo de vida útil de los activos, referenciados en normas internacionales como API 1160, AME B31.8, ASME B 31.8S y decretos supremos DS N° 081-2007-EM , entre otros.
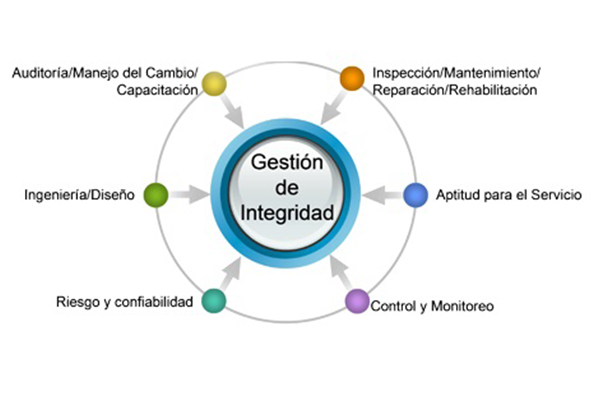
- Adecuación al Decreto Supremo DS N° 081-2007 – Reglamento de Transporte de Gas Natural.
- Adecuación al Decreto Supremo DS N° 042-199 – Reglamento de Distribución de Gas Natural.
- Consultoría en Integridad de Plantas y equipos.
- Programas de Inspección y Mantenimiento de Plantas y Equipos
- Integridad de equipos e instalaciones
- Generación de Plan de Mantenimiento a Corto Mediano y Largo Plazo.
- Análisis de Riesgo Cuantitativo, Semi-cuantitativo y Cualitativo.
- Caracterización de materiales.
- Servicio de Capacitaciones
La empresa brinda capacitaciones In House en:
- Implementación de Sistemas de Integridad de Ductos.
- Sistemas de Protección Catódica por Corriente Impresa y Galvánica.
- Monitoreo y control de la corrosión interna.
- Metodología ECDA, ICDA y SCCDA.
- Inspecciones Indirectas CIS, DCVG, Resistividad de Suelos y PCM.
- Instalación, configuración y Puesta en Marcha en Sistemas de Monitoreo Remoto para Protección Catódica.
- Mantenimiento de Rectificadores.
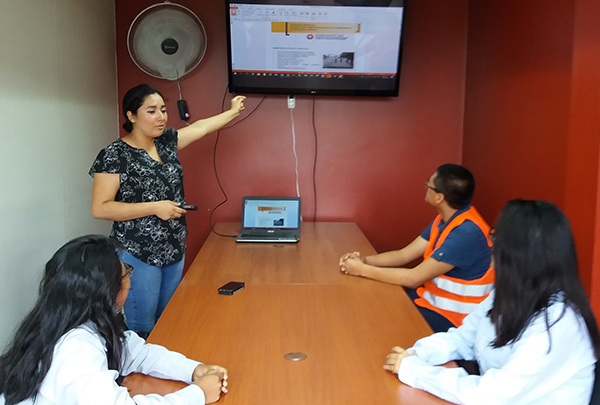
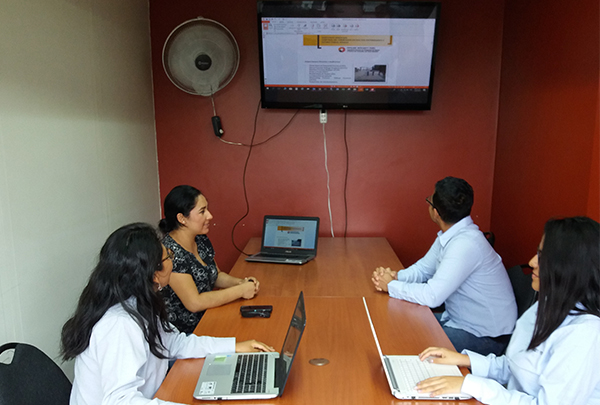
- Ensayos No Destructivos
- Tintes Penetrantes:
Este ensayo consiste en detectar imperfecciones superficiales en materiales no porosos tanto en materiales metálicos como en materiales no metálicos. Este tipo de ensayo consiste básicamente en la aplicación de un líquido de gran poder humectante sobre la superficie del material a ensayar. Gracias al efecto de la capilaridad, éste penetrará en las discontinuidades. Finalmente el sobrante que resta sobre la superficie será retirado mediante un sistema de limpieza adecuado y la posterior aplicación de un revelador será capaz de volver a extraer el líquido que antes quedó atrapado en las discontinuidades, mostrando la localización de las mismas.
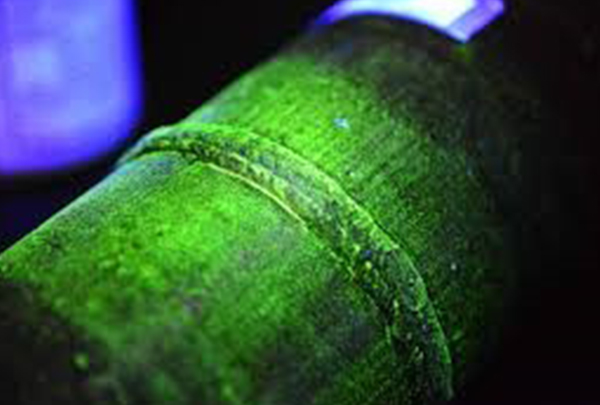
- Radiografía Industrial:
Consiste en atravesar el componente a ensayar con un haz de radiación electromagnética ionizante (rayos gamma o rayos X). Esta radiación será más o menos absorbida por las discontinuidades internas de la pieza, llegando a la otra cara de la misma, con una intensidad de radiación distinta, e impresionando una película radiográfica, la cual, una vez revelada muestra la localización de dichas discontinuidades.
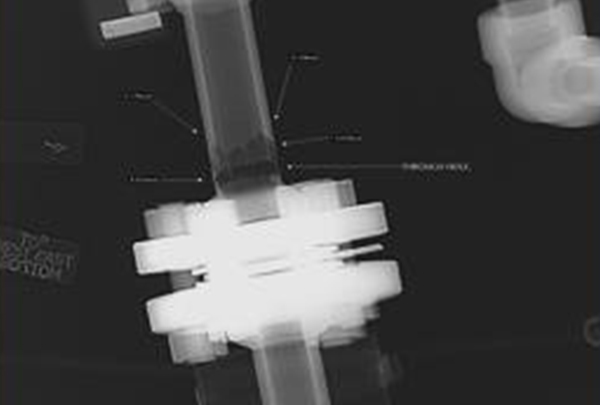
- Ultrasonido Convencional y Avanzado:
El ensayo por ultrasonidos es un método de Ensayo No Destructivo que se fundamenta en el fenómeno de la reflexión de las ondas acústicas cuando se encuentran con discontinuidades en su propagación. La onda será reflejada hasta su fuente de generación si la discontinuidad se encuentra en una posición normal en relación al haz incidente.
- Ultrasonido Convencional:
Los equipos de Ensayos Convencionales de Ultrasonido trabajan con el principio del envío de un haz pulsado de ultrasonido de alta frecuencia a partir de un transductor de mano o palpador, que se coloca sobre la superficie del objeto que va a ser ensayado. En la inspección manual el Inspector actúa directamente en la ejecución del examen, o sea, es responsable de la correcta aplicación de los procedimientos de inspección, tanto en la manipulación de los palpadores como en la interpretación de los datos.
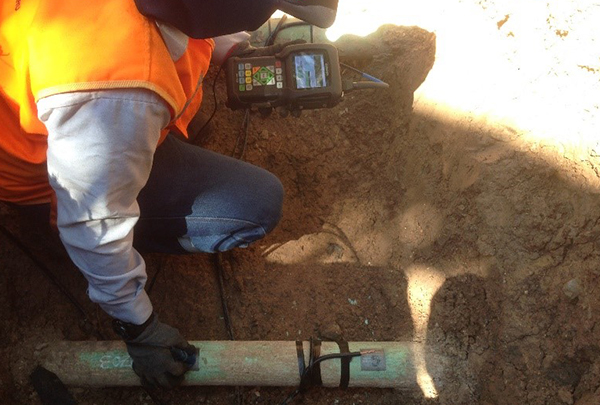
- Ultrasonido Avanzado:
Es el método pulso-eco, se realiza dividiendo la soldadura en zonas y empleando para cada una de ellas un palpador especifico. Este método de trabajo implica emplear un palpador para cada zona, variando el número de ellos según el perfil y espesor de la soldadura. Los palpadores, montados sobre un carro, se desplazan en sentido circunferencial en torno a la soldadura manteniendo una distancia constante con respecto a la línea central de la misma.
Los ensayos de ultrasonido aportan algunas ventajas significativas tales como:
• Minimizar el tiempo entre la ejecución del ensayo y el informe de resultados, permitiendo la corrección inmediata de defectos sistemáticos en el proceso y, en consecuencia, reducir el número de reparaciones.
• No emplear fuentes radiactivas, siendo innecesaria, por tanto, la delimitación de zonas de exclusión de personal y pudiendo realizar el ensayo próximo al frente de soldadura.
• Mayor capacidad de detección de defectos lineales tales como las faltas de fusión.
• Permitir la localización de los defectos en profundidad, facilitando el proceso de reparación.
• Permitir el dimensionamiento de los defectos en altura, para así poder emplear criterios alternativos de aceptación, como, por ejemplo, el Engineering Critical Assessment (Evaluación Crítica de Ingeniería).
- Partículas Magnéticas:
Estos ensayos tienen la misión de detectar en una pieza las posibles discontinuidades (en materiales ferromagnéticos) que haya no solo en la superficie, sino también en las proximidades de ella (discontinuidades subsuperficiales).
El método se basa en la atracción de un polvo metálico aplicado sobre la superficie hacia las discontinuidades presentes en el material bajo la acción de un campo magnético. La acumulación de este polvo metálico en torno a las discontinuidades revelará la localización de las mismas.
Esta peculiaridad hace que este ensayo pueda realizarse en ciertas circunstancias a piezas pintadas o con imprimación.
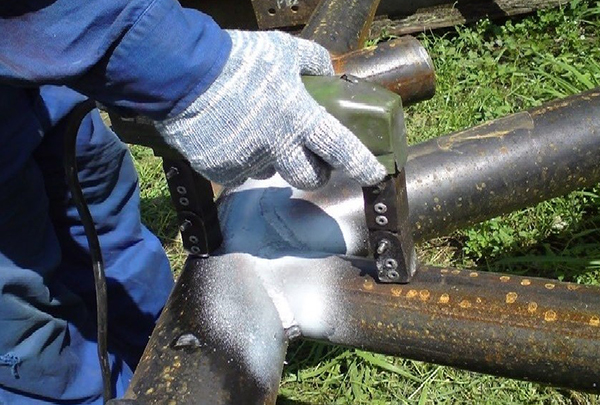
- Inspección Visual:
El ensayo de inspección visual es un método de ensayo no destructivo que permite la detección de discontinuidades que afectan a la superficie visualmente accesible de los objetos.
La inspección visual es el método no destructivo por excelencia, siendo su alcance de aplicación extremadamente extenso:
• Identificar materiales respecto a su especificación y composición química.
• Detección de imperfecciones y defectos producidos durante un proceso productivo.
• La inspección visual no solo es importante como método de ensayo en sí mismo, sino que es esencial como ensayo previo y preliminar en la ejecución de cualquier otro. Ya que debe realizarse siempre, incluso cuando esté prevista la ejecución de otro tipo de ensayos.
• Bien ejecutado reduce la necesidad de END posteriores.
Para poder realizar eficazmente el ensayo visual, es tan importante saber realizar técnicamente la observación visual, como saber interpretar los resultados observados. Los conocimientos de materiales, procesos de fabricación y utilidades de uso de los componentes ensayados son esenciales. Según los instrumentos que se utilicen como ayuda a la visión, y la distancia (o el acceso) que se tenga entre el inspector y el objeto de estudio, la Inspección Visual se puede dividir en dos grupos.
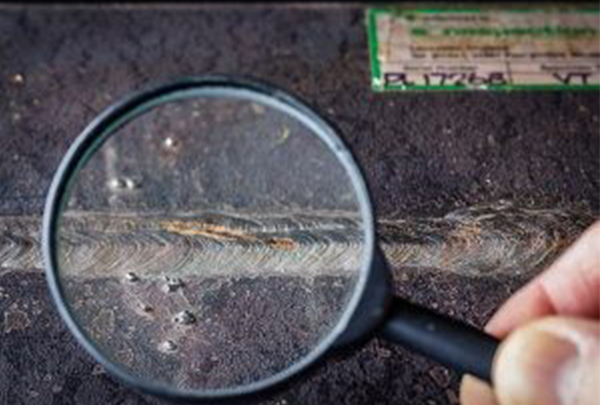
- Prueba de Holiday:
Esta técnica consiste en determinar discontinuidades presentes en recubrimientos de protección no conductores aplicados sobre substratos metálicos.
Mediante equipo digital portátil Holiday de alto y bajo voltaje se realiza medición de continuidad del recubrimiento en los equipos, líneas de tubería entre otros.
• El recubrimiento debe estar debidamente seco y curado según los tiempos recomendados por el fabricante antes de ejecutar el ensayo.
• La superficie debe estar limpia, seca y libre de aceite, suciedad u otros contaminantes.
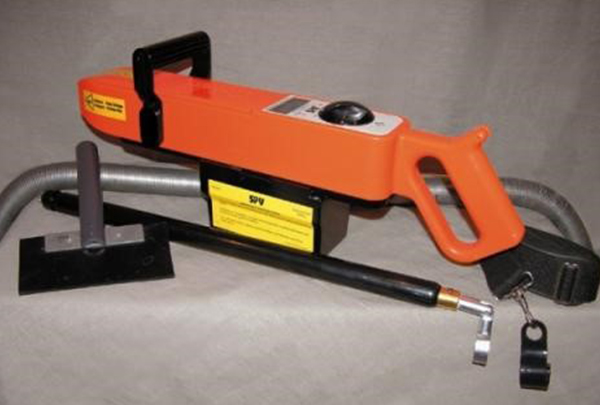
- Pruebas Destructivas
- Pruebas de Ensayo de Tensión:
Ensayo utilizado para medir la resistencia de un material a una fuerza estática o aplicada lentamente. Esta prueba consiste en alargar una probeta de ensayo por fuerza de tensión, ejercida gradualmente, con el fin de conocer ciertas propiedades mecánicas de materiales en general.
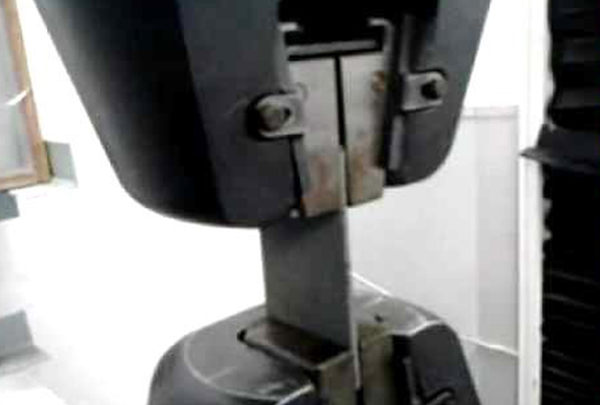
- Prueba de Doblez:
Consiste en aplicarle a una probeta una fuerza constante, doblándose en forma de U en el centro de la soldadura. La superficie convexa de la curvatura se examina en busca de grietas u otros defectos. Se utiliza para evaluar la calidad de la soldadura (ductilidad y sanidad) de un material, como evidencia de su capacidad para resistir el agrietamiento durante el doblez.
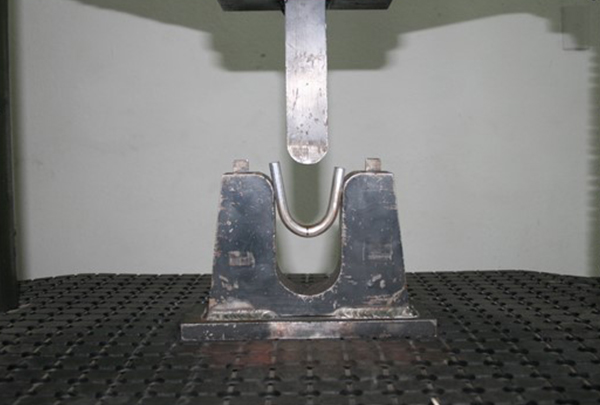
- Prueba de Impacto:
Las pruebas de impacto tienen objetivo de determinar cuanta energía absorbe un material ante un impacto bajo condiciones específicas.
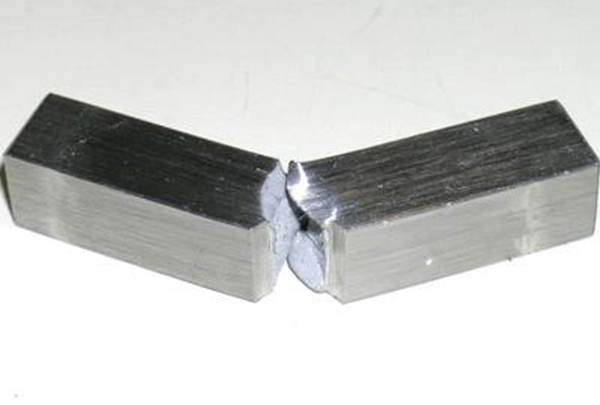
- Pruebas de Nick-Break:
La prueba NICK-BREAK es útil para determinar la calidad interna del metal de soldadura. Esta prueba revela defectos internos (si está presente), tales como inclusiones de escorias, bolsas de gas, falta de fusión. La prueba consiste en romper por algún medio hasta romper la soldadura entallada como muestra la figura.
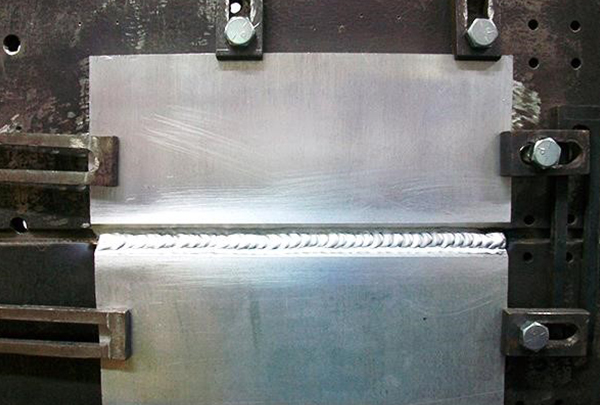
- Ensayo de Macrografía:
La macrografía verifica entre otros la ausencia de defectos, determinar la geometría de la unión soldada o poder observar el grado de penetración de los cordones de soldadura en el material base. La detección de defectos en las uniones soldadas es de vital importancia para poderlos corregir y evitar que se utilicen construcciones que puedan llegar a fallar durante su uso, ocasionando daños materiales o, incluso, personales.
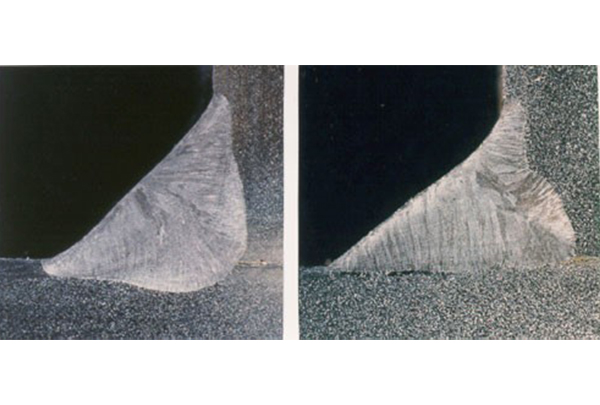
- Supervisión y Asesoría en Soldadura
La importancia de resultados satisfactorios en cualquier proyecto hace necesario que exista una supervisión técnica durante el desarrollo de las actividades, esta debe ser realizada por personal adiestrado e independiente a aquellos que realizan el servicio de fabricación y montaje. Esto no intenta diluir o reemplazar la clara responsabilidad de la o las compañías que realizan los trabajos de fabricación, montaje e inspecciones, sino encaminar un proceso de mejora continua, por lo que las supervisiones se han implementado como práctica común en todo tipo de proyectos a nivel global, de tal modo que son referidas en diferentes normativas y códigos de carácter técnico.
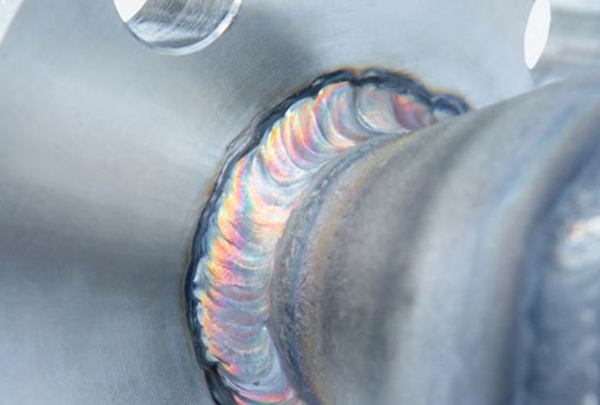
- Servicio de Caracterización de Materiales
- Identificación positiva de materiales (PMI):
El análisis positivo de materiales, PMI (Positive Material Identification) es un Ensayo No Destructivo que abarca un amplio campo de aplicaciones en la industria: desde la fundición los materiales metálicos y fabricación de los equipos hasta la inspección de los mismos en servicio. Es un método necesario tanto para la clasificación de chatarra, como para averiguar el material que se ha de emplear en una eventual reparación de un equipo.
Son industrias especialmente receptoras de este servicio: acerías, fundiciones, industrias de automoción, talleres de mecanización, talleres de calderería, oleoductos, gaseoductos, centrales para generar energía, refinerías, etc...
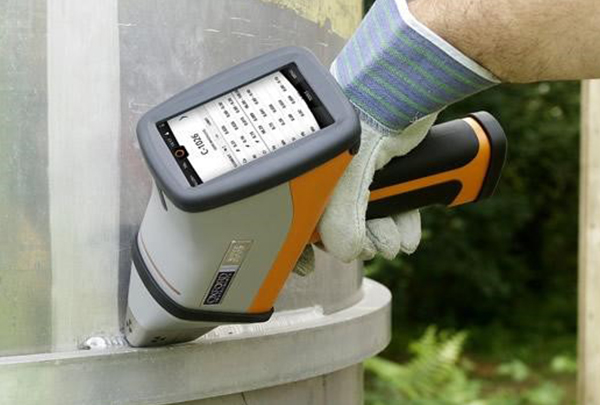
- Metalografía:
La metalografía es la parte de la metalurgia que estudia las características estructurales o de constitución de los metales y aleaciones, para relacionarlas con las propiedades físicas, mecánicas y químicas de los mismos. La importancia del examen metalográfico radica en que, aunque con ciertas limitaciones, es capaz de revelar la historia del tratamiento mecánico y térmico que ha sufrido el material. A través de este estudio se pueden determinar características como el tamaño de grano, distribución de las fases que componen la aleación, inclusiones no metálicas como sopladuras, micro cavidades de contracción, escorias, etc., que pueden modificar las propiedades mecánicas del metal. En general a partir de un examen metalográfico bien practicado es posible obtener un diagnóstico y/o un pronóstico.
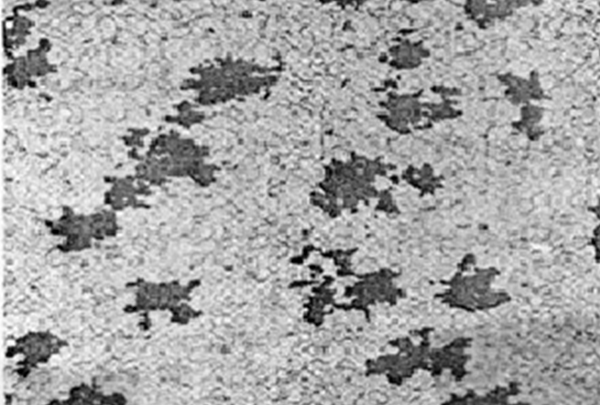
- Replicas Metalográficas:
La replicación metalográfica, es empleada para llevar a cabo la evaluación in situ de la microestructura de determinados componentes y materiales. Entendiendo evaluación como la determinación del deterioro o daño sufrido por un determinado material que ha sido consecuencia de un determinado proceso de fabricación o al que se le ha sometido a un servicio determinado en unas condiciones ambientales concretas.

- Medición de Dureza:
La dureza de un determinado material es la medida de la resistencia de un material a la deformación plástica localizada. Las técnicas cuantitativas de medida de la dureza que se basan en un pequeño penetrador que es forzado sobre una superficie del material a ensayar en condiciones controladas de carga y velocidad de aplicación.
Se mide la profundidad o tamaño de la huella resultante, lo cual se relaciona con un número de dureza.
• Medición de durezas en diferentes puntos de componentes y materiales.
• Obtención de medidas mediante durómetro portátil.
• Ensayos de dureza Rockwell.
• Ensayos de dureza Brinell.
• Determinación de durezas previas y posteriores a tratamientos térmicos de materiales y soldaduras.